Single-acting hydraulic cylinder
Einfachwirkender Hydraulikzylinder SR
Single-acting hydraulic cylinders are one of the most basic and commonly used types of hydraulic cylinders. They are particularly known for their simple design, reliability and cost-effectiveness. In this article, we take a closer look at the functionality, design and typical applications of a single-acting hydraulic cylinder.
1. Funktionsweise eines einfach wirkenden Hydraulikzylinders
A single-acting hydraulic cylinder only exerts force in one direction, usually in the forward movement (extension of the piston). The piston is returned by an external force, e.g:
- Gravity,
- an integrated return spring,
- a mechanical or external load.
The movement is based on the principle of hydraulics, in which a non-compressible fluid (hydraulic oil) is pressurized. This pressure is transferred to the piston surface, creating a linear movement.
Movement sequence:
- Hydraulic oil is pressed into the cylinder via a connection.
- The piston moves outwards and generates force.
- As soon as the pressure escapes, the piston moves back to its starting position due to external forces.
2. Aufbau eines einfach wirkenden Hydraulikzylinders
The design of a single-acting hydraulic cylinder is relatively straightforward. It comprises the following main components:
- Cylinder barrel: A robust housing, usually made of steel or aluminum, which contains the piston and the hydraulic fluid.
- Piston: The moving component that is pushed outwards by the hydraulic pressure.
- Piston rod: A rod that is connected to the piston and transmits the movement to the outside.
- Seals: They prevent hydraulic fluid from escaping and protect the cylinder from contamination.
- Return mechanism (optional): Some single-acting cylinders are fitted with a spring that automatically returns the piston when the pressure escapes.
3. Vorteile eines einfach wirkenden Hydraulikzylinders
Single-acting hydraulic cylinders offer numerous advantages that make them particularly attractive in cost-sensitive and less complex applications:
- Simple design: Fewer components mean lower manufacturing costs and easy maintenance.
- Compact design: The absence of a second pressure connection means that these cylinders save space.
- Cost efficiency: Due to their simple design, they are cheaper to purchase and repair.
- Longevity: Fewer moving parts mean less chance of failure.
4. Einschränkungen von einfach wirkenden Hydraulikzylindern
However, this simplicity also comes with some limitations:
- Movement in one direction only: A single-acting cylinder is unsuitable for applications that require precise control in both directions.
- Dependence on external forces: The return of the piston depends on external factors such as gravity or a return spring, which can limit flexibility.
- Less versatility: Compared to double-acting cylinders, the areas of application are limited.
5. Typische Anwendungsbereiche
Single-acting hydraulic cylinders are mainly used where only one direction of force is required and the return stroke can be supported by external forces:
- Agriculture: For lifting trailers or controlling tipping mechanisms.
- Construction industry: In lifting platforms or hydraulic jacks where gravity takes over the return stroke.
- Mechanical engineering: In simple pressing machines that only require a pressure movement.
- Transportation: For lifting and lowering loading rails or ramps.
6. Beispiel: Hydraulischer Wagenheber
A common example of the use of a single-acting hydraulic cylinder is the hydraulic jack. When a vehicle is lifted, hydraulic fluid is pumped into the cylinder under pressure, causing the piston rod to move outwards. As soon as the pressure is released, gravity ensures that the piston returns to its starting position.
7. Conclusion
Single-acting hydraulic cylinders are essential for applications that require force in one direction and where the piston can be returned naturally or by a spring. Their simple design, reliability and cost-effectiveness make them a preferred choice in many industrial and mechanical processes. However, when designing a hydraulic system, the specific requirements of the application should be considered to ensure that a single-acting cylinder is the optimum solution.
Double-acting hydraulic cylinder
Doppelt wirkender Differentialzylinder EKPS
Double acting hydraulic cylinders are among the most versatile and most frequently used types of hydraulic cylinders. They enable precise control of movement in both directions and are used wherever both pushing and pulling movements are required. In this article, we explain in detail how a double-acting hydraulic cylinder works, how it is constructed and in which applications it is particularly useful.
1. Funktionsweise eines doppelwirkenden Hydraulikzylinders
In contrast to single-acting cylinders, a double-acting hydraulic cylinder generates force in both directions of movement - both when extending and retracting. This is made possible by the use of two separate hydraulic connections:
- Pressure connection A: Presses hydraulic fluid onto the piston surface to extend the piston.
- Pressure connection B: Presses liquid onto the back of the piston to retract it.
The movement is controlled by a hydraulic control valve that regulates the flow of hydraulic fluid between the two connections.
Movement sequence:
- Hydraulic fluid is pressed into the cylinder via connection A → The piston extends.
- To retract, the hydraulic fluid is fed in via connection B and drained via connection A → The piston retracts.
2. Aufbau eines doppelt wirkenden Hydraulikzylinders
A double acting hydraulic cylinder is more complex than a single-acting cylinder and consists of the following main components:
- Cylinder barrel: Contains the piston and the hydraulic fluid.
- Piston: The central component that is moved by hydraulic pressure. The piston is equipped with seals to separate the pressure on both sides of the cylinder.
- Piston rod: Transmits the movement of the piston to external devices.
- Seals: Ensure sealing between piston, piston rod and cylinder barrel.
- Two connections: One for the forward pressure (A) and one for the reverse pressure (B).
- End caps: Close the cylinder at both ends and serve as fixing points.
3. Vorteile eines doppelwirkenden Hydraulikzylinders
Double-acting hydraulic cylinders offer numerous advantages that make them indispensable for a wide range of applications:
- Power in both directions: Enables precise control and a wide range of applications.
- High efficiency: The piston can retract and extend independently of external forces.
- Smooth movement: The constant pressure flow ensures smooth and controlled movements.
- Flexibility: Can be used in horizontal, vertical and even overhead positions.
- High load capacity: Suitable for heavy loads and demanding tasks.
4. Einschränkungen von doppelt wirkenden Hydraulikzylindern
Despite their versatility, double-acting hydraulic cylinders also have some limitations:
- Complexity: Construction and maintenance are more complex compared to single-acting cylinders.
- Costs: Due to the additional components and connections, they are more expensive to purchase.
- Hydraulic system dependency: Requires a constant supply of hydraulic pressure in both directions.
5. Typische Anwendungsbereiche
Double-acting hydraulic cylinders are used wherever precise movements and force in both directions are required. The most common applications include
- Construction and forestry machinery: Excavators, wheel loaders, bulldozers and log splitters.
- Industrial production: Pressing, punching, mold making and material handling.
- Agriculture: Control of plows, mowers and balers.
- Cranes and lifting platforms: For precise lifting and lowering of heavy loads.
- Marine and offshore applications: Control of anchor winches, hatches and hydraulic arms.
6. Example: Excavator arm
A classic example of the use of a double-acting hydraulic cylinder is the arm of an excavator. The cylinder controls the raising and lowering of the arm, whereby force is required in both directions:
- When extended, the arm lifts loads.
- When retracting, it lowers the arm in a controlled manner or retracts the bucket.
7. Besondere Varianten von doppelwirkenden Hydraulikzylindern
There are special variants of double-acting cylinders that are optimized for specific applications:
- Differential cylinder: The piston surface is larger on one side in order to achieve different forces and speeds in the directions of movement.
- Tandem cylinders: Two or more cylinders work together to achieve higher forces or greater movement paths.
- Synchronous cylinder: Developed to precisely coordinate parallel movements with multiple cylinders.
8 Important selection criteria
The following points should be considered when selecting a double-acting hydraulic cylinder:
- Maximum lifting force and working pressure.
- Stroke: How far should the piston be able to travel?
- Operating temperature and ambient conditions.
- Installation and mounting: Does the cylinder need to be permanently installed or mobile?
9. Conclusion
Double-acting hydraulic cylinders are indispensable for applications that require force and movement in both directions. Thanks to their versatility, reliability and precise control options, they are used in almost all industries. Proper selection and maintenance are critical to maximize the life and efficiency of these cylinders. If you are planning a special application, it is best to consult an expert to find the optimum cylinder for your needs!
Telescopic cylinder
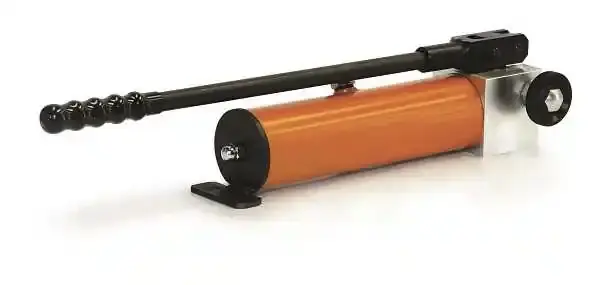
Einfachwirkender 1-stufiger Handpumpenzylinder PH1
Telescopic cylinders, also known as multi-stage cylinders or plunger cylinders, are a special type of hydraulic cylinder characterized by their multi-stage design. This enables particularly long stroke lengths with a compact design when retracted. They are often used in applications where large movement distances are required but installation space is limited. In this article, we explain how telescopic cylinders work, their design and the most important areas of application.
1. Funktionsweise eines Teleskopzylinders
Telescopic cylinders consist of several interlocking cylinder stages that extend one after the other like the segments of a telescope. Each stage is smaller than the previous one, which considerably increases the range of movement without the cylinder taking up too much space when retracted.
The movement is usually hydraulic:
- Extension: Hydraulic fluid is pressed into the first stage, causing the largest piston stage to extend. As soon as this is fully extended, the next stage is activated. This process is repeated until all stages are extended.
- Retract: The pressure is built up in the opposite direction so that the stages are retracted one after the other. The return movement is often assisted by gravity in the case of single-acting telescopic cylinders.
Telescopic cylinders can be either single-acting or double-acting:
- Single-acting: The steps are returned by gravity or external forces.
- Double-acting: The pressure is also used to retract the cylinder stages, which enables more precise control.
2. Aufbau eines Teleskopzylinders
The design of a telescopic cylinder differs from standard cylinders due to its multi-stage construction. The main components are
- Cylinder barrel: The outer part that encloses the largest stage of the cylinder.
- Steps: Several interlocking cylinder segments that extend one after the other.
- Piston: Each stage has its own piston with seals to control hydraulic fluid between the stages.
- Piston rod: The smallest and last stage that is connected to the moving load.
- Seals: Provide a seal between the steps and prevent leaks.
- Connections: For the supply and discharge of hydraulic fluid.
3. Vorteile von Teleskopzylindern
The unique design of telescopic cylinders offers a number of advantages:
- Long stroke with compact design: Ideal for applications with limited space but large movement requirements.
- Flexibility: Can be used in vertical, horizontal and inclined positions.
- Reduced size: When retracted, telescopic cylinders are considerably shorter than conventional cylinders with the same stroke.
- Versatile configurations: Available as single-acting or double-acting, depending on requirements.
- High performance: Constant power transmission is guaranteed even with long lifting distances.
4. Einschränkungen von Teleskopzylindern
However, the complex design of telescopic cylinders also entails some limitations:
- Complexity: The design is more complicated than standard cylinders, which leads to higher manufacturing costs.
- Sensitivity: The interlocking stages can be more sensitive to lateral forces and dirt.
- Maintenance requirements: Due to the large number of seals and moving parts, maintenance requirements may be higher.
- Uneven force: The force transmission varies between the stages, as the effective piston cross-section becomes smaller with each extended stage.
5. Typische Anwendungsbereiche
Telescopic cylinders are used in numerous industries and applications, especially where long stroke lengths and compact design are crucial:
- Construction industry: Lifting devices for tippers, cranes and concrete pumps.
- Transportation: Refuse collection vehicles that require high lifting movements to empty containers.
- Heavy-duty applications: Mobile cranes and lifting platforms that have to move heavy loads to considerable heights.
- Agriculture: Lifting systems for trailers or heavy equipment.
- Offshore and shipping: Use in confined spaces on ships or in oil and gas extraction.
6. Beispiel: Kippmechanismus eines LKWs
A typical example of the use of a telescopic cylinder is the tipping mechanism of a truck:
- When loading, the cylinder is compactly retracted so that it takes up little space.
- During unloading, the cylinder is extended to raise the loading surface and tip the material.
- After unloading, the cylinder retracts again and returns the loading platform to its starting position.
7. Besondere Varianten von Teleskopzylindern
There are special variants of telescopic cylinders that are tailored to specific requirements:
- Synchronized telescopic cylinders: Designed to extend all steps simultaneously and ensure smooth movement.
- Multi-stage cylinder with integrated spring: For applications that require automatic return without hydraulic pressure.
- High-pressure telescopic cylinders: For applications where very high forces are required.
8 Important selection criteria
The following factors should be taken into account when selecting a telescopic cylinder:
- Stroke and size: How much movement is required and how compact does the cylinder need to be?
- Operating pressure: Is the cylinder designed for the required pressure rating?
- Operating conditions: Environmental influences such as temperature, humidity or dirt.
- Type of load: Are lateral forces or extreme loads to be expected?
9. Conclusion
Telescopic cylinders are an ideal solution for many industrial and mobile applications due to their ability to achieve long strokes in a small space. Their versatility and efficiency make them indispensable in areas such as construction, transportation and agriculture. Despite their higher cost and complexity, they offer decisive advantages when compact design and long movement distances are required. Anyone requiring a telescopic cylinder for a specific application should carry out a detailed analysis of the requirements in order to find the right solution.
Differential cylinder
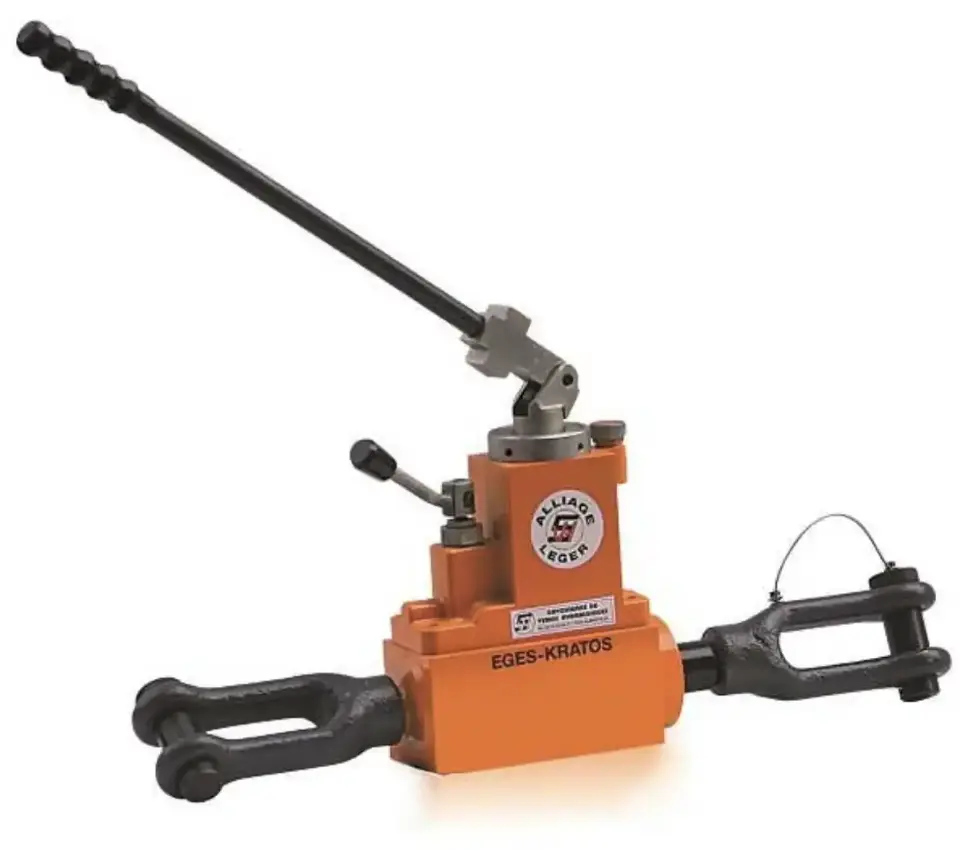
Differentialzylinder mit eingebauter Pumpe EKPI.A
Differential cylinders are a special type of double-acting hydraulic cylinders that are characterized by their asymmetrical design. They offer particular advantages in applications where different speeds and forces are required in the directions of movement. In this article, we explain in detail how a differential cylinder works, how it is constructed and where it is most commonly used.
1. Funktionsweise eines Differentialzylinders
The differential cylinder differs from conventional double-acting cylinders in the size of the piston surfaces on both sides of the piston. The full piston area (without piston rod) acts on the front of the piston, while the rear has a smaller effective area as the piston rod takes up space. This leads to an asymmetrical movement:
- Extension: When hydraulic fluid is pushed into the front chamber, the piston extends slowly as the entire surface of the piston is used, generating a high force.
- Retracting: During the return stroke, hydraulic fluid is pumped into the rear chamber. As the effective area is smaller, the piston retracts faster, but with less force.
This behavior - slower and more powerful when extending, faster and less powerful when retracting - is the hallmark of the differential cylinder.
2. Aufbau eines Differentialzylinders
A differential cylinder is constructed in a similar way to a double-acting cylinder, but with a decisive difference in the geometry of the piston surfaces. The main components are:
- Cylinder tube: Contains the chambers for the hydraulic fluid.
- Piston: The moving component that converts pressure into movement. The piston is designed so that there is a smaller area on the back (due to the piston rod).
- Piston rod: A solid rod that is connected to the piston and transmits the movement to the outside. Its surface area reduces the effective area at the rear.
- Seals: Provide a seal between the two chambers and prevent leaks.
- Hydraulic connections: Two connections for the supply and discharge of hydraulic fluid.
3. Vorteile eines Differentialzylinders
The differential cylinder offers several advantages due to its asymmetrical design:
- Different speeds: Enables slow and powerful forward movement and faster reverse movement, reducing cycle time in many applications.
- Efficient power transmission: High forces during extension make it ideal for heavy-duty applications.
- Space saving: Due to the smaller size compared to symmetrical cylinders with the same output.
- Flexibility: Can be operated both horizontally and vertically.
4. Einschränkungen eines Differentialzylinders
Despite its advantages, the differential cylinder also has some limitations:
- Asymmetrical forces: The different force in the directions of movement can be a disadvantage in certain applications.
- More complex control: Controlling the fluid flow requires more precise valve technology to control the movement efficiently.
- Limited application possibilities: Not suitable for applications that require uniform forces and speeds in both directions.
5. Typische Anwendungsbereiche
Differential cylinders are used in numerous industrial and mobile applications where there are different movement requirements in the two directions:
- Construction machinery: In excavator arms, shovels and cranes where slow lifting and fast lowering of loads is required.
- Agricultural machinery: Control of plows, harrows and other implements where power and speed must vary.
- Manufacturing and automation: Machines that perform cyclical movements, such as presses or cutting machines.
- Loading and tipping mechanisms: For lifting and lowering loads on vehicles such as tippers and refuse collection vehicles.
- Forestry: Timber grapples and splitting machines that require high forces for splitting and faster returns.
6. Example: Wood splitter
A common example of the use of a differential cylinder is the log splitter:
- Extension: The piston moves slowly and with high force to split wood.
- Retract: The piston moves back quickly to position the next log, reducing the cycle time.
7. Besondere Varianten von Differentialzylindern
There are special versions of differential cylinders that are tailored to specific applications:
- Synchronized differential cylinders: Developed to operate several cylinders in parallel in one application.
- High-pressure differential cylinders: For applications with extreme loads, such as in heavy industry or mining.
- Mini differential cylinders: For compact machines and mobile devices where space is limited.
8 Important selection criteria
The following aspects should be considered when selecting a differential cylinder:
- Strength requirements: How much force is required for forward and backward movement?
- Speed: What speed is required in both directions of movement?
- Size: Is the available space for the cylinder limited?
- Operating conditions: Temperature, humidity and possible contamination of the environment.
9. Conclusion
Differential cylinders are an excellent choice for applications that require different forces and speeds in the directions of movement. Their compact design and efficient power transmission make them particularly attractive for mobile machines and cyclical processes. Despite their limitations, they offer clear advantages over other cylinder types in the right applications. If you are planning a hydraulic system, it is worth carefully analyzing the specific requirements to ensure that a differential cylinder is the optimum solution.
Plunger cylinder
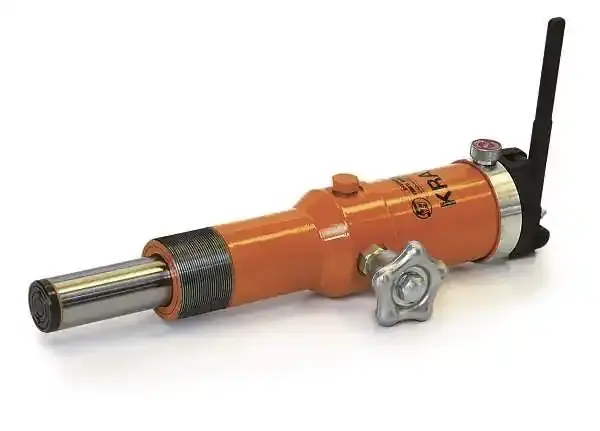
Federzylinder mit Einbaupumpe KLPS-KLPI
Plunger cylinders, also known as rod cylinders or pressure cylinders, are a special type of hydraulic cylinder that do not require a classic piston. They are characterized by their robust design and their ability to transmit high forces. These cylinders are often used in heavy industrial applications and in the construction industry. In this article, we explain how plunger cylinders work, their design and the most important areas of application. Translated with DeepL.com (free version)
1. Funktionsweise eines Plungerzylinders
In contrast to conventional hydraulic cylinders, the plunger cylinder does not have a piston inside the cylinder tube. Instead, the hydraulic pressure acts directly on the end face of the piston rod (also known as the plunger). The movement is purely linear and depends on the hydraulic fluid supplied.
Movement sequence:
- Extending: Hydraulic fluid is pressed into the cylinder, causing the pressure to act directly on the face of the piston rod. The rod moves outwards.
- Retracting: In most cases, retraction is achieved by gravity, an external load or in some cases by a return spring, as plunger cylinders are usually single-acting.
2. Aufbau eines Plungerzylinders
The design of a plunger cylinder is comparatively simple, which contributes to its robustness and durability. The main components are
- Cylinder barrel: The housing that contains the hydraulic fluid and provides the guide for the piston rod.
- Piston rod (plunger): A solid, cylindrical rod that is moved directly by the hydraulic pressure.
- Face: The area of the piston rod on which the pressure acts.
- Seals: Prevent hydraulic fluid from escaping and protect against contamination.
- Connection: A single hydraulic connection for supplying the fluid.
- Guide bearing: Supports the piston rod and prevents it from bending under high loads.
3. Vorteile eines Plungerzylinders
Plunger cylinders offer numerous advantages, especially in applications that require high pressures and robust solutions:
- High load capacity: Ideal for applications with extremely high loads and pressures.
- Simple design: Fewer moving parts mean less maintenance and a longer service life.
- Compact design: Due to the lack of pistons, plunger cylinders can be designed to save space.
- Versatility: Can be operated in vertical or horizontal orientation.
- Low weight: Compared to cylinders with pistons, the design is lighter, which is particularly advantageous in mobile applications.
4. Einschränkungen eines Plungerzylinders
Despite their strengths, there are some limitations when using plunger cylinders:
- No double-acting function: As a rule, plunger cylinders are single-acting, which means that the return of the rod depends on external forces.
- Dependence on gravity: Most models require gravity or a load to ensure the return stroke, which can limit their applications.
- Lateral forces: Plunger cylinders are more sensitive to lateral forces and require precise alignment.
- Limited controllability: The return movement can be controlled less precisely than with double-acting cylinders.
5. Typische Anwendungsbereiche
Plunger cylinders are used in a variety of industrial and mobile applications where high forces are required in a small area. The most common areas of application include
- Construction industry: Hydraulic lifting devices, lifting platforms, bridge lifting systems and pile drivers.
- Industrial presses: Applications where very high forces are required, such as in metal forming or punching.
- Heavy-duty applications: For lifting and lowering heavy machines or vehicles.
- Maritime applications: In ships and offshore installations, e.g. for hatch lifters or lifting platforms.
- Agriculture: Heavy equipment such as balers or plows that require a high lifting force.
6. Beispiel: Schwerlasthebebühne
A common example of the use of a plunger cylinder is the heavy-duty lifting platform:
- When lifting vehicles or machines, hydraulic fluid is pressed into the cylinder, causing the solid piston rod to move slowly upwards.
- Once the lifting process is complete, gravity or the weight of the load ensures that the piston rod returns to its starting position.
7. Besondere Varianten von Plungerzylindern
There are special versions of plunger cylinders that are tailored to specific applications:
- Telescopic plunger cylinder: Combination of telescopic and plunger cylinders for particularly long lifting distances in a compact design.
- High-pressure plunger cylinders: For extreme loads and high pressures, e.g. in heavy industry.
- Stainless steel plunger cylinders: For corrosion-prone environments such as offshore or chemical applications.
8 Important selection criteria
The following aspects should be considered when selecting a plunger cylinder:
- Lifting force and working pressure: How much force must be transmitted?
- Stroke: How far should the piston rod be able to extend?
- Operating environment: Are special materials (e.g. stainless steel) required?
- Type of load: Are high lateral forces or other loads to be expected?
9. Conclusion
Plunger cylinders are a robust and efficient solution for applications that require high forces but do not need a double-acting function. Their simple design, high load capacity and long service life make them a preferred choice in the construction industry, mechanical engineering and heavy-duty applications. Despite some limitations, such as the dependence on external forces for the return stroke, they remain indispensable in many areas. For specific applications, it is advisable to carefully analyze the requirements in order to select the ideal plunger cylinder.
Special cylinder
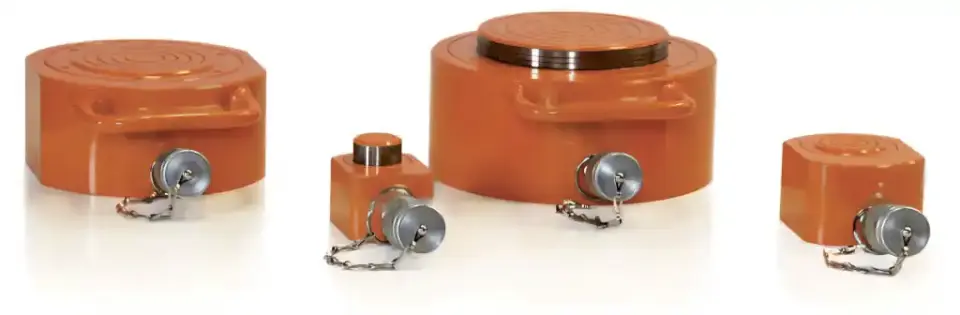
Ultra-Flachzylinder einfachwirkend (UB)
Special cylinders are custom-made hydraulic cylinders that are tailored precisely to the requirements of a specific application. They go beyond standard solutions and often combine elements of different cylinder types to overcome unique technical challenges. Special cylinders play a central role in applications that require special movements, forces or environmental requirements. In this article, we take a look at how special cylinders work, their design and typical areas of application.
1. Funktionsweise eines Sonderzylinders
The functionality of a special cylinder varies greatly, as it depends on the specific requirements. As a rule, special cylinders are based on the principles of conventional hydraulic cylinders (single-acting, double-acting, telescopic or plunger cylinders) and are enhanced with additional functions, materials or designs.
Examples of special functions:
- Precise motion control: use of positioning sensors and integrated electronics.
- Combination of linear and rotary movements: Cylinders that can not only push, but also rotate.
- High-precision force control: For applications where very precise forces are required, e.g. in medical technology.
- Multiple control: Integration of several cylinder functions in one component.
2. Aufbau eines Sonderzylinders
The design of a special cylinder depends on the specific requirements of the application and can vary greatly. Common modifications and extensions include
- Special materials: Use of stainless steel, titanium or other special alloys for corrosive, hygienic or extreme environments.
- Unusual dimensions: Extra-long stroke lengths, compact designs or unusual diameters.
- Additional sensors: Integrated position and pressure sensors for precise control.
- Multi-chamber systems: Allow different movements or forces in a single cylinder.
- Special seals: For extreme temperatures, chemical resistance or minimal friction.
- Combination with other technologies: Electrical or pneumatic components to extend functionality.
3. Vorteile eines Sonderzylinders
Special cylinders offer a number of advantages that make them indispensable for demanding applications:
- Customized solutions: Perfectly tailored to the specific requirements of the application.
- Greater efficiency: Optimized performance thanks to adapted design.
- Increased functionality: Integration of several functions in one cylinder reduces the space requirement and the complexity of the overall system.
- Durability: Use of high-quality materials and precise manufacturing for demanding conditions.
- Flexibility: Adaptable to almost any application, regardless of the technical requirements.
4. Einschränkungen eines Sonderzylinders
The customized design of special cylinders also has some disadvantages:
- Higher costs: Due to individual development and production, special cylinders are more expensive than standard solutions.
- Longer development time: Planning, production and testing take more time.
- Complexity: Maintenance and repair can be more complicated, as spare parts and know-how must be specific.
- Limited reusability: Special cylinders can often not be used in other applications.
5. Typische Anwendungsbereiche
Special cylinders are used in a variety of specialized industries and applications, including:
- Automotive industry: control of test benches, active suspension systems and high-precision presses.
- Medical technology: Cylinders for surgical devices or diagnostic machines that require maximum precision and hygiene.
- Aerospace: Cylinders for flight control systems, landing gear or space technology that have to withstand extreme conditions.
- Offshore and underwater technology: Hydraulic cylinders for deep-sea applications that can withstand high pressure and corrosive conditions.
- Robotics and automation: Cylinders with integrated sensors and controls for highly dynamic motion sequences.
- Energy technology: In hydroelectric power stations or for controlling turbines and valves.
6. Beispiel: Sonderzylinder in der Offshore-Technik
A typical example of the use of a special cylinder is the control of underwater robots (ROVs) in the offshore industry:
- Materials: Use of corrosion-resistant alloys such as stainless steel or titanium.
- Seals: Special high-pressure seals that can withstand a pressure of several 100 bar.
- Sensors: Integrated sensors for monitoring position, pressure and temperature.
- Functionality: Combination of linear movements and rotary movements for controlling gripper arms.
7. Besondere Varianten von Sonderzylindern
There are numerous types of special cylinders that are tailored to specific applications:
- Combination cylinder: Combination of linear and rotary movements in one component.
- Welding cylinder: Especially for welding applications with high temperatures and flying sparks.
- Hygienic cylinders: For the food or pharmaceutical industry with special cleaning and surface finish requirements.
- High-pressure cylinders: For applications with exceptionally high operating pressures.
- Miniature cylinders: For precise applications with minimal space requirements.
8 Important selection criteria
The development of a special cylinder requires a precise analysis of the requirements. The most important criteria include
- Forces and lifting distances: What forces and movements are required?
- Operating conditions: Temperature, moisture, corrosion, dirt or chemical effects.
- Material requirements: Do special materials have to be used?
- Additional functions: Are sensors, electrical components or special motion sequences required?
- Maintenance and service life: How often does the cylinder need to be serviced and what is the target service life?
9. Conclusion
Special cylinders offer tailor-made solutions for the most demanding applications that could not be realized with standard cylinders. Their versatility, precision and robustness make them an indispensable component in sectors such as aviation, medical technology and the offshore industry. Despite higher costs and longer development times, their performance and reliability justify the expense. If you need a special cylinder, close collaboration with an experienced manufacturer is crucial to develop the ideal solution for your requirements.